The feed method of thread turning is determined by the cutting machine tool, workpiece material, blade geometry and the pitch of the thread being machined. There are usually four feed methods as follows:
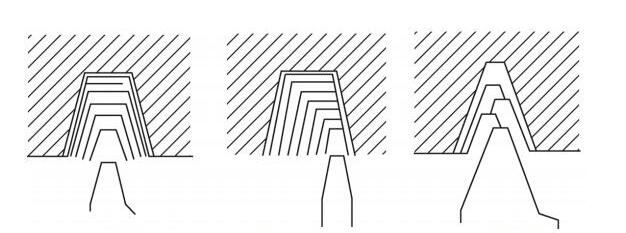
1. Commonly used cutting method-left and right turning at the same time. In this method the axial cutting component force received is offset, which partially overcomes the phenomenon of turning tool deviation caused by the axial cutting component force. Both sides wear uniformly, which can ensure the clear tooth shape. But have problems such as poor chip evacuation, poor heat dissipation, and concentrated force.
2. The single-side feed tool feeds and cuts at an angle with the radial direction. The chips are rolled away from the blade to form strips, which have better heat dissipation. The disadvantage is that the other edge hardens due to not cutting
3. Cutting on both sides of the blade to form rolled chips, smooth chip removal, good heat dissipation, and low thread surface roughness. Generally speaking, this is a good method for turning stainless steel, alloy steel and carbon steel. About 90% of threaded materials use this method. If this method is used for thread processing on a CNC lathe, a canned cycle can generally be called, which is easy to program.
4. The left and right sides feed alternately and cut left and right alternately. That is, each time it is in radial feed, it moves a certain distance laterally to the left or right, so that only one side of the turning tool participates in cutting. This method is more complicated to program on CNC lathes.
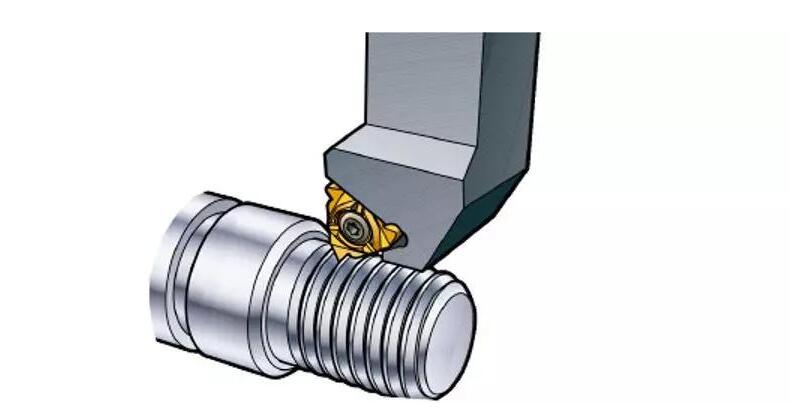
Thread milling is mainly used for CNC boring and milling machine such as machining centers. Generally, small-diameter internal threads (20mm) can be processed by tapping, but for the processing of large-diameter internal threads and external threads, there are many problems with tapping and sleeve threads.
Thread milling is different from thread turning. This is because thread CNC milling is mainly realized by the three-axis linkage and spiral interpolation processing of the machine tool. That is, while the two-axis is used for arc milling, the third-axis is used for machining. Linear feed motion, its axial movement distance milling processing, is single-edge milling processing, so its feed method generally adopts the radial direct feed cutting method, so that the two cutting edges cut at the same time, the force is more uniform, and the thread can be guaranteed Accuracy, and CNC programming is relatively simple.
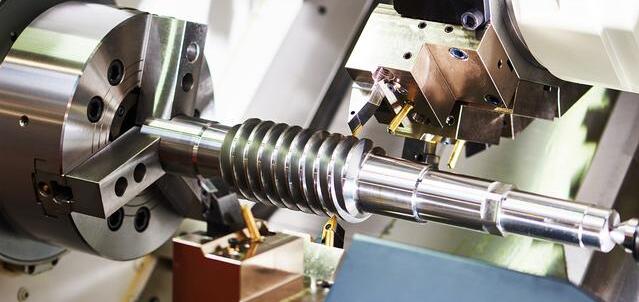
In the cutting process, the tool wears quickly and the tool life is short. The cutting speed is too fast, the cooling is insufficient, the number of cuts is too much, and the blade grade is incorrect. It can be used to reduce the cutting speed, fully cool, reduce the number of cutting, choose high hardness wear-resistant blades and good toughness blades, change the cutting angle, increase cooling, increase the cutting speed, and reduce the amount of back-grabbing.
Excessive plastic deformation of the tool is caused by poor cooling, too high cutting speed, incorrect blade grade, and too much back-grabbing each time. Should reduce the amount of back-grabbing, increase cooling, reduce cutting speed, increase cutting times, use high hardness, wear-resistant hard alloy or Xu layer blades.
There is a burr on the top of the thread. To increase the cutting speed, use the automatic centering principle with a cutting centering chuck to clamp the workpiece for processing. Bearing brackets with different center heights can be adjusted by adding pad irons, but they need to be fastened by bolts.
Dalian Indus Machinery Technology Co.,Ltd
-www.indmt.com